Klean Kanteen is Measuring What Matters
It’s hard to imagine, but back in the early 2000s you couldn’t buy a reusable stainless steel water bottle in the United States. Plastic was pretty much the only option. We sold the first BPA free, stainless steel bottles in 2004, and today reusable water bottles are everywhere!
Klean Kanteen has become an international brand and has inspired dozens of other companies to make reusable stainless steel products. Here at Klean Kanteen we take a holistic approach to understanding and managing the environmental footprint of our products — from sourcing raw materials to manufacturing, packaging, shipping, daily use, and end-of-life disposal. We call this Measuring What Matters.
To do this, we use a lifecycle assessment process and other tools that uncover hidden impacts and track our progress year over year. This information allows us to identify improvements that can lower a product’s overall environmental impact without sacrificing performance. Here are just a few highlights of our processes in action:
First of all, did you know one vacuum insulated stainless steel bottle requires twice the resources to produce as a single-wall bottle of the same size? It’s true! In 2019, the switch to a new manufacturing partner for our next generation of insulated products reduced the amount of water needed to manufacture the TKWide collection, bringing it closer to the water usage of single-wall. Through similar changes, greenhouse gas emissions per unit of purchased electricity have also been reduced due to the amount of energy in our manufacturing supply chain that comes from cleaner sources such as natural gas and solar. The Klean design and sourcing teams continue to work on manufacturing solutions that conserve resources, while still delivering the award-winning Climate Lock™ vacuum insulation you love.
When we discovered how much paper went into boxing individual retail products, we moved to “packaging” all of our Kanteens in belly bands or hang tags only. This simple switch saves substantial amounts of water and material every year and produces fewer greenhouse gas emissions!
Where the paper for our belly bands, packaging material and shipping boxes comes from matters, too. Right now 100% of our paper material is made from post-consumer recycled content and/or forest-friendly materials that are certified by the Forest Stewardship Council.
We also assess the impacts of shipping our products from the factory to our headquarters in Chico, California. We learned just how much more greenhouse gas emissions air freight produces than container ship. In fact, although we only used air freight to ship 1-2% of the total weight coming to our headquarters in 2018, it accounted for 25- 35% of our transport emissions! Through careful planning, we have since reduced our use of air freight by 62%.
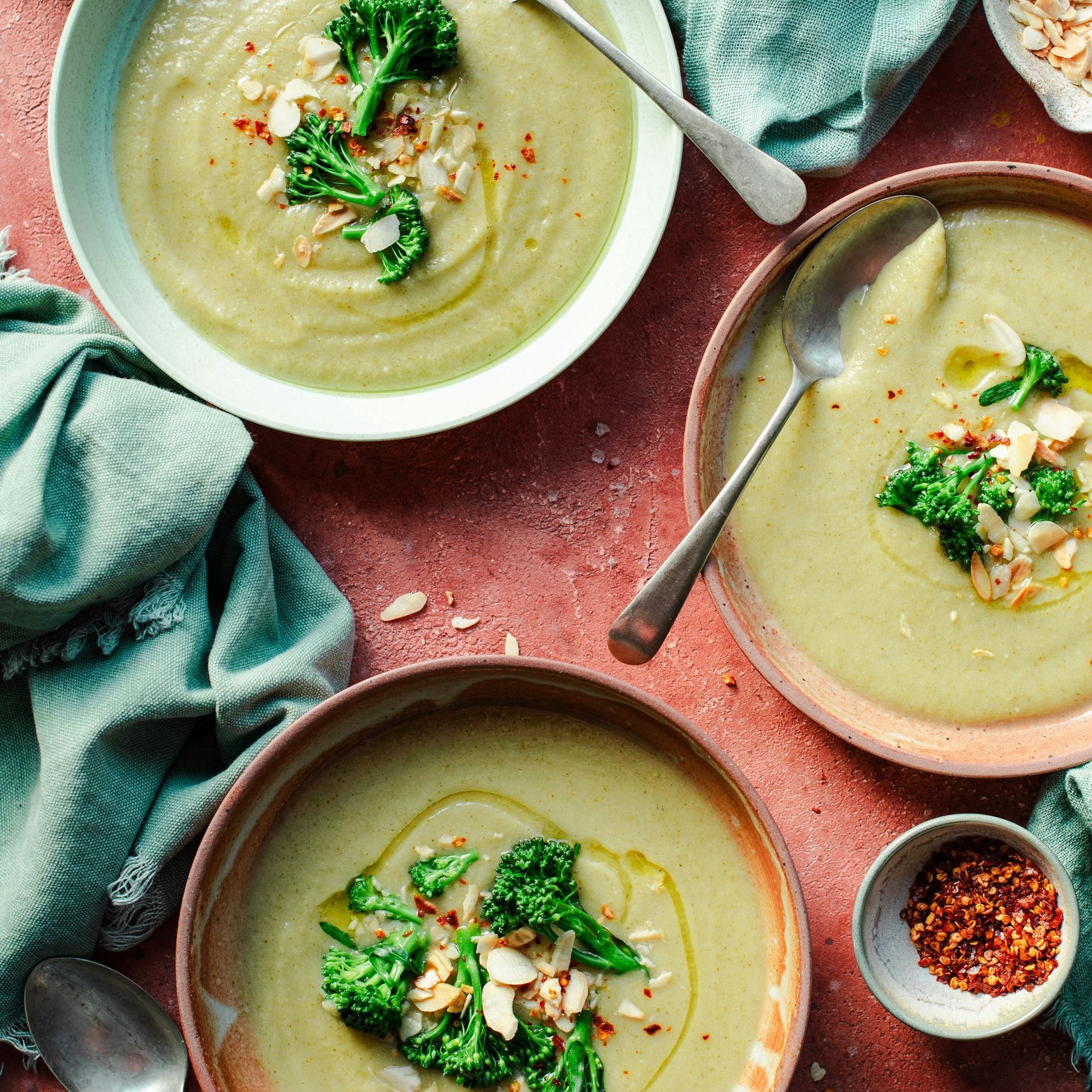
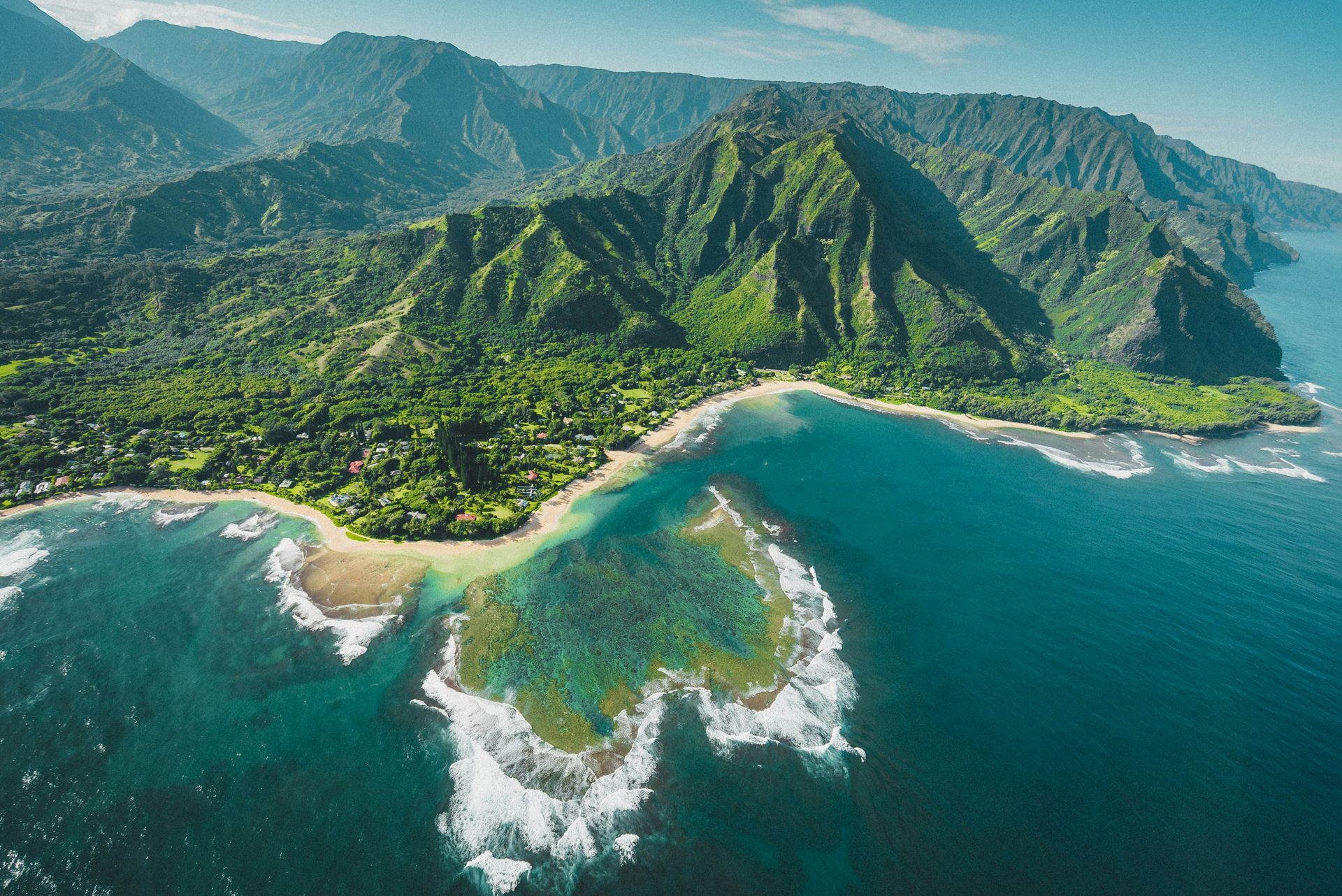
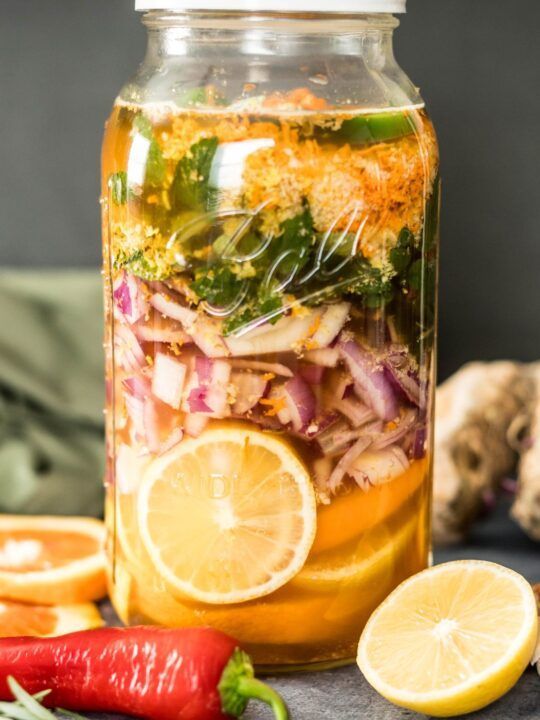
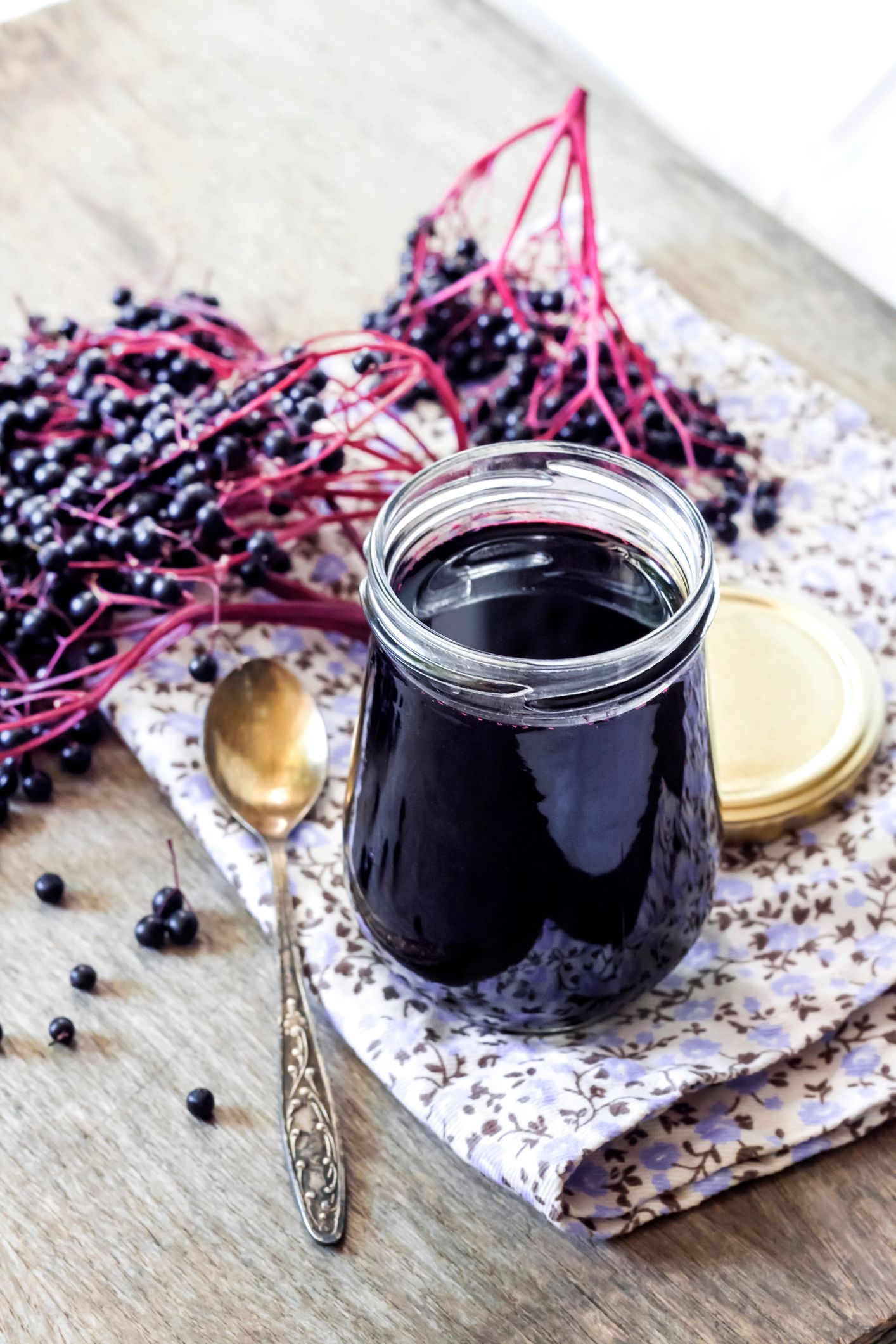
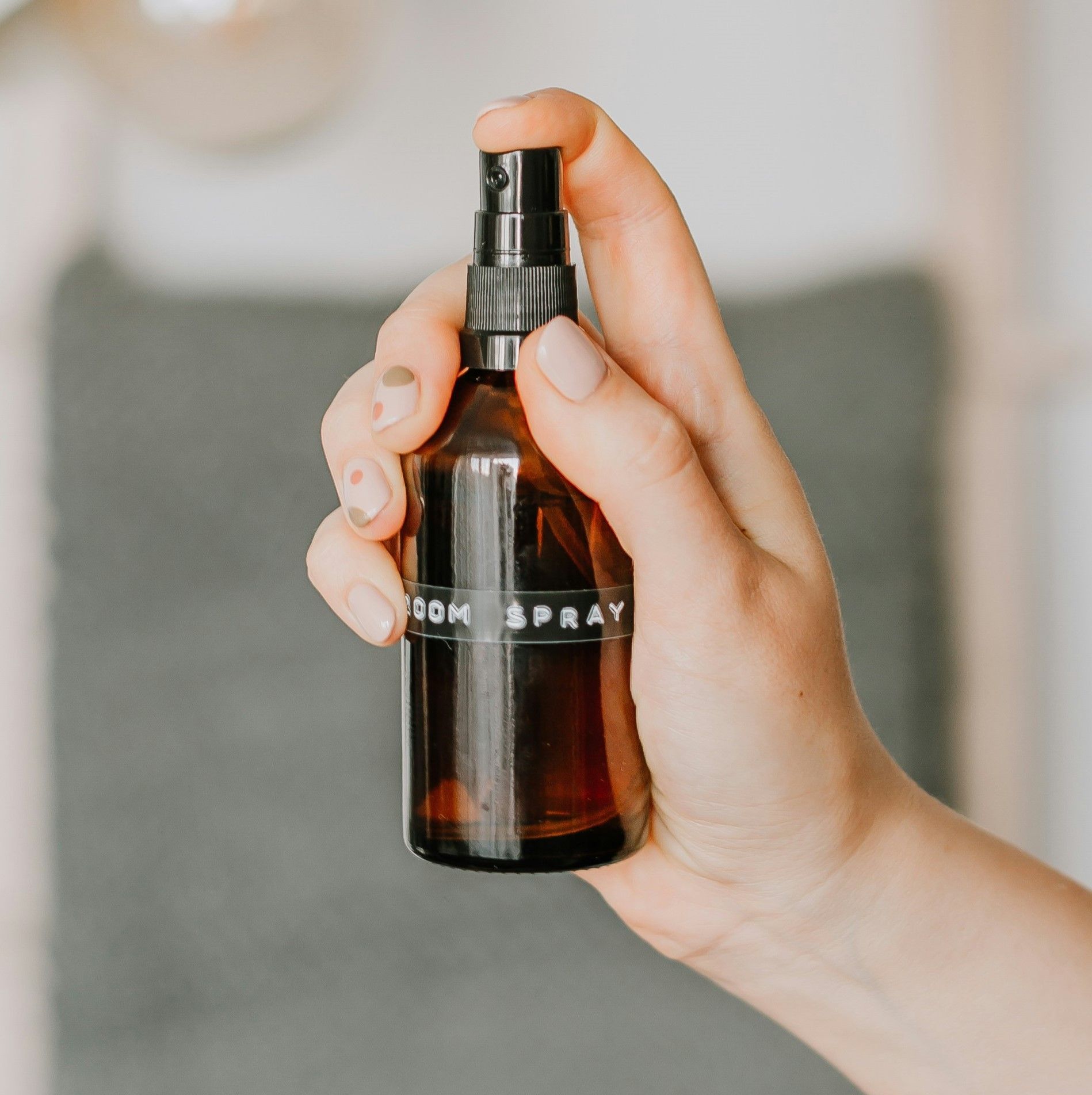
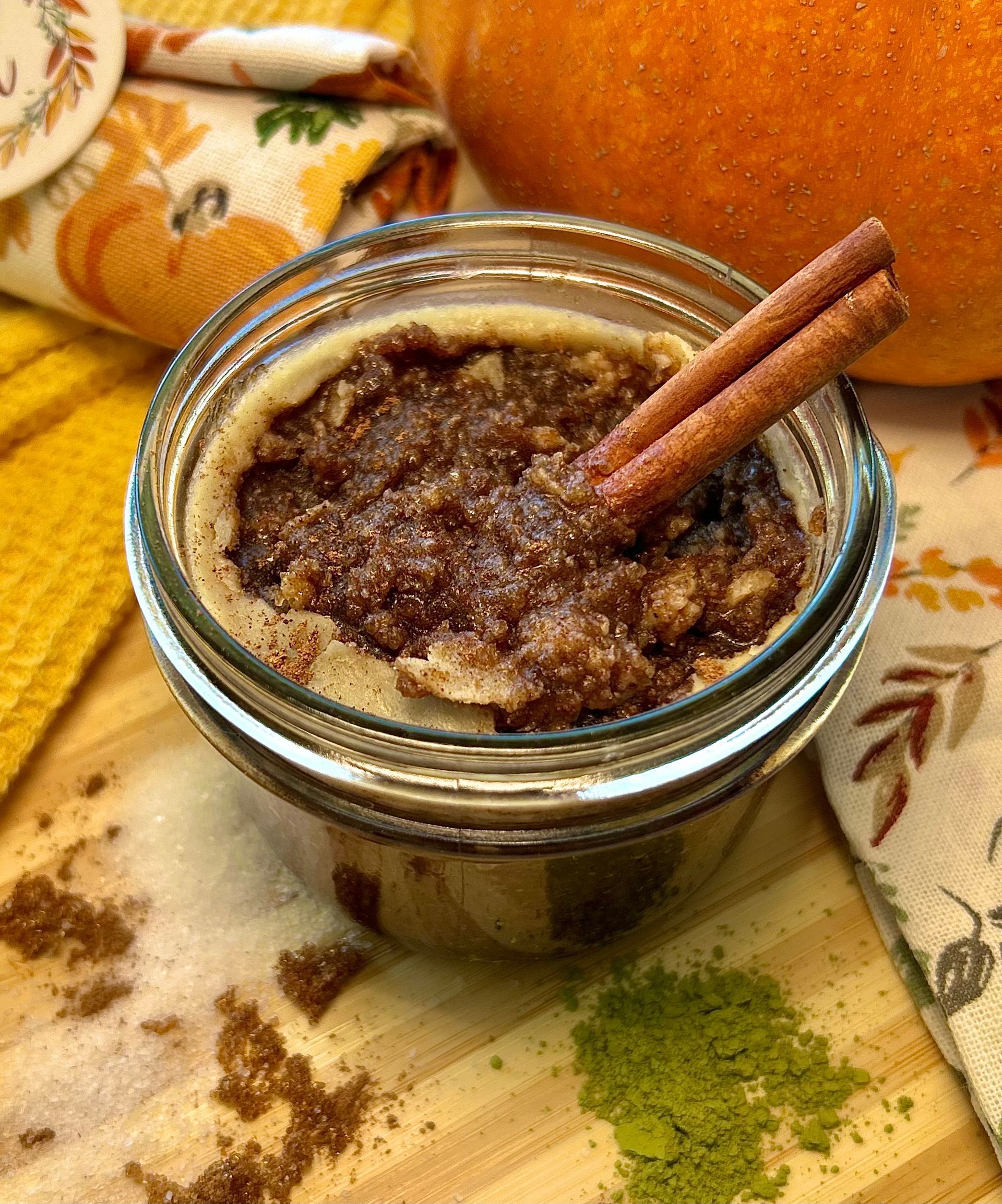
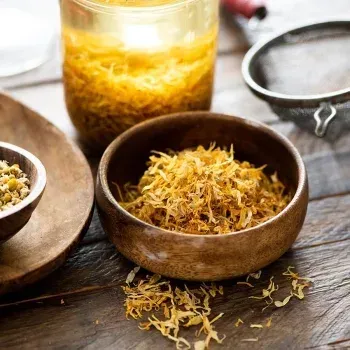